IT ALL COMES DOWN TO THE RIGHT PACKAGING WHEN SHIPPING TEMPERATURE-SENSITIVE PRODUCTS
Laboratories and hospitals have to transport items on a regular basis, whether it’s blood supplies, laboratory samples, vaccines, medicines, or even organs. But unlike conventional shipped goods, these items need to be well protected during transport and, in most cases, reliably chilled. That’s why customers opt for the temperature-controlled packaging developed and, upon request, customized by manufacturers such as Storopack, the protective packaging specialist based in Metzingen.
Active vs. Passive
There are two options for keeping temperature-sensitive goods cool: active and passive. Active coolant requires energy, provided for example by the transport vehicle. This solution makes sense in food logistics when large quantities are transported, for instance in the air-conditioned cargo space of a truck. But this means that all of the goods have to be transported within the same temperature range. If some of the goods need to be cooled at a lower temperature, a separate refrigerated space becomes necessary, for example in a two-chamber vehicle. Because it’s comparatively more expensive, active coolant is not always worthwhile in the pharmaceutical and laboratory sector, with its smaller shipments.
Passive coolant offers much better value for money in the form of thermoboxes with plastic cooling packs, gel cushions, or foam bricks, which reliably maintain the temperature of shipped goods within a certain range for a defined period of time. According to Thomas Thein, Business Unit Manager Medical Europe at Storopack, this offers several benefits for the sender: “Shipping with a thermobox can be much cheaper than with active coolant, for example in the truck’s air-conditioned cargo space. You’re also on the safe side particularly when shipping in regions that can’t necessarily guarantee a consistent power supply.” Manufacturers such as Storopack not only offer many standard boxes, but also pre-qualified system solutions in different sizes, with defined temperature ranges, and for specific transport durations. If you don’t find what you’re looking for, Storopack can also develop a tailored solution based on the customer’s needs. “The pharmaceutical and biotechnology sectors primarily opt for 24-hour thermal packaging with a temperature range of 2 to 8°C or 15 to 25°C in Germany, Austria, Switzerland, and neighboring European countries. But there are also solutions for 48 hours or longer,” says Thomas Thein. “There’s a high demand for thermal packaging with longer cooling periods, including for international shipping in regions in which truck transport is out of the question, for example overseas.”
What do you need to think about when choosing packaging?
It’s not only your own requirements in terms of safety, hygiene, and quality that should play a role when choosing temperature-controlled packaging. Pharmaceutical manufacturers and their logistics departments have to meet the Good Distribution Practice (GDP) requirements, the guidelines of the European Commission, to ensure the quality and integrity of medicinal products. Laboratories are familiar with these requirements and have taken the necessary steps to accommodate them. These can also be a criterion when choosing a suitable protective packaging specialist. Once a manufacturer has been found, we recommend answering a few basic questions to quickly identify the ideal product for temperature-controlled shipping:
- How long will it take for the package to reach its destination?
- Will the package be shipped nationally or internationally?
- What will the climatic conditions be during transport?
- Which temperature range needs to be maintained during shipment?
- Does a disposable or reusable solution make more sense?
- What volume is required?
- Is the product so sensitive that the transport box needs to be especially durable?
- Are there any size or weight restrictions for the package, for example to ensure better handling?
- Which method of shipment was chosen? Airfreight, by truck?
If there is any doubt, the protective packaging manufacturer can advise you, as confirmed by Thomas Thein: “We discuss with the customer all of the factors associated with temperature-controlled transport, including the anticipated climatic conditions in transit, the transport times, and which coolants make sense.”
When you need a customized thermobox
Temperature-controlled shipping frequently requires customized solutions – the packaging is developed from scratch for the customer, with the form and coolant tailored specifically to the product to be transported. This is where Storopack comes in, offering a consultation at the customer’s location. First the solution requirements are identified, and then a 3D design and CAD drawing prepared. Storopack then produces a prototype of the box, which is used for further testing. Finally, experts put the solution through its paces in the company’s own testing area. “The environmental chamber simulates the changing thermal environmental conditions during transport and can reproduce scenarios in the range of –25 to +50°C,” explains Olaf Neumann, Product Manager at Storopack. With 2.5 square meters of space and a height of 2.75 meters, it can also hold an industrial pallet. “Several data loggers are positioned throughout the packaging for the tests and record temperature curves. The prototype also undergoes practical testing in the form of actual shipment.” If it performs well, the box goes into production and is then ready for delivery and use.
What is a pre-qualified system solution?
We recommend pre-qualified system solutions if there’s no desire or need for a tailormade box, as manufacturers offer standard ranges featuring suitable solutions. Storopack has an exact definition of what that means: “For us, pre-qualified means that the box type was developed to document performance in accordance with the European AFNOR NF S99-700 standard and tested in the environmental chamber with a summer and winter scenario,” says Olaf Neumann. Tests like these are carried out without any transport goods in the packing space, which represents a worst-case scenario for temperature-controlled packaging. The average temperature is 26°C in the summer scenario and 7°C in the winter scenario.
The results of the environmental chamber tests are recorded in a qualification report that accompanies the system solution. Customers thus have proof that, for example, a 24-hour system solution in the range of 2 to 8°C can reliably maintain the temperature for this period of time – even with fluctuating ambient temperatures. Storopack also directly supplies all of the other components required for temperature-controlled shipment: thermobox, coolant, outer box, inner box (payload), and packing instructions. Small disposable or reusable data loggers can also be incorporated into the packaging to monitor the temperature along the entire cold chain. An integrated USB port makes it possible to evaluate the data at the destination. Storopack offers pre-qualified system solutions for temperature-controlled transport in different temperature ranges with a cooling period of 24, 48, 96 or 120 hours. If the shipment is too small for a complete truck load, but too large for individual insulated boxes, customers can also opt for a thermo pallet shipper, a plug-in solution that fits perfectly on a conventional Euro pallet. Special phase change material (PCM) freezer packs maintain the desired temperature and, thanks to phase change, can store and release hot and cold energy for long periods of time.
Conclusion
Passive coolant is a reliable, cost-effective way for laboratories, pharmacies, pharmaceutical manufacturers, and general suppliers and senders in the pharmaceutical and biotechnology sectors to ship temperature-sensitive goods. Suitable options include thermoboxes and pre-qualified system solutions that can maintain the temperature of the packaged goods within the desired range for up to several days. If required, protective packaging manufacturers can also develop customized solutions for temperature-controlled and safe shipment of a product. Innovative providers such as Storopack also take into account new standards such as the GDP guidelines.
What do you value in a thermobox?
“For our purposes, a thermobox needs to reliably maintain a temperature between 2 and 8°C for at least 48 hours. The box also needs to be lightweight, sturdy, recyclable, and not too expensive. The solution should also fulfill the GDP standards and be suitable for products in accordance with the GMP standards. Passive coolant offers many benefits for us, as it means we’re no longer dependent on individual logistics providers or the mode of transport, be it by air or truck. The flexibility of passive coolant is an essential factor particularly in areas in which speed plays a key role, such as shipments containing organic sample materials.”
- Sylvia Weimer-Hartmann, CEO and owner of Biokanol Pharma
Image: Biokanol Pharma GmbH, Rastatt
Thermobox Material
Depending on requirements and temperatures during transport and storage, insulated box systems can be made of either EPS, EPP, Neopor® or hybrid material – a combination of EPS and PE or EPS and PP. The industry is also pursuing the development of materials that are 100 percent compostable.
EPS (expanded polystyrene), which is commonly referred to as Styropor®, combines several benefits all at once: it’s very lightweight because it contains 98 percent air, exceptionally pressure-resistant, and absorbs next to no water. Due to the low thermal conductivity of the material, temperature-sensitive products are very well protected. The material is also completely recyclable, so it can be used again for added benefit.
Neopor® boasts outstanding heat and cold insulation properties, high compressive strength, shock absorption, low weight, and moisture resistance. Neopor® boxes are therefore often used for shipping pharmaceutical products. The material also features infrared absorbers and reflectors, which unlike conventional insulation materials can reduce thermal conductivity.
EPP (expanded polypropylene) is particularly robust, durable, and lightweight. EPP is the ideal basis for a tailored, reusable packaging solution, as the extremely durable material can withstand strain such as shocks and even repeated impacts during transport – EPP remains fully functional.
Hybrid material is an intelligent combination of EPS and PE (polyethylene) or EPS and PP (polypropylene), and therefore combines the benefits of these materials: the low density of EPS and the exceptional chemical resistance and shock absorption of PE or PP. It’s even tougher and more abrasion-resistant than EPS, so that boxes made of hybrid material can be used especially when the conditions are more demanding or if they need to withstand repeated use.
Order temperature-controlled packaging online
Customers can access the standard range at www.storopack-shop.de, with a variety of thermoboxes and system solutions, including boxes specifically developed for the pharmaceutical, biotechnology, trade, pharmacy, logistics, and food industries. When selecting a standard box, it’s important to consider both the desired size and the wall thickness, which ranges from 20 to 50 millimeters. The longer the product needs to be chilled, the thicker the wall should be.
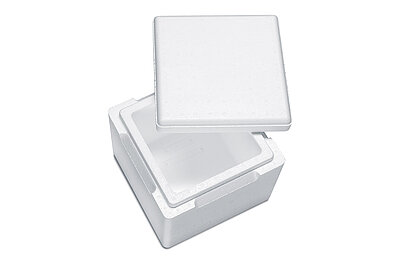
Storopack Hans Reichenecker GmbH
Untere Rietstrasse 30
72555 Metzingen
T +49 (0)7123 164-0